Effective warehouse space management is crucial for optimizing operations and maximizing profitability. Poor management can lead to decreased productivity, efficiency, and safety, significantly impacting a business’s bottom line.
Importance of Effective Warehouse Space Management
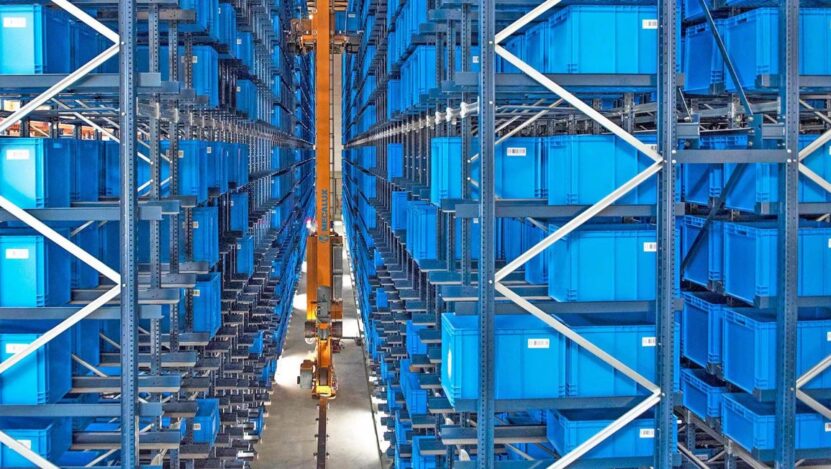
Effective warehouse space management ensures that every square foot of the warehouse is utilized efficiently. This leads to streamlined operations, increased productivity, and improved safety.
By optimizing the use of space, businesses can handle more inventory, fulfill orders faster, and reduce operational costs. Well-managed warehouse space can prevent bottlenecks, reduce the risk of accidents, and ensure a smoother workflow.
Effective space management helps in maintaining an organized warehouse, which simplifies inventory tracking and improves the accuracy of order picking. Overall, efficient warehouse space management is essential for maintaining high levels of operational efficiency and profitability.
Common Issues Caused by Poor Warehouse Management
Poor warehouse management can cause a range of issues that negatively impact productivity, efficiency, and safety. For instance, inadequate storage solutions can lead to overcrowded spaces, resulting in order backlogs and stock build-ups.
Obstructed pathways due to cluttered inventory can create hazardous working conditions and slow down operations. Inefficient use of space can also lead to longer picking times, increased labor costs, and delayed order fulfillment.
These issues not only reduce overall efficiency but also hurt profitability by increasing operational costs and reducing customer satisfaction.
Furthermore, poor warehouse management can result in higher rates of damaged goods, leading to additional losses and decreased customer trust.
Identifying Storage Problems
Identifying storage problems early can prevent significant operational disruptions. Warning signs of inadequate storage space include frequent order backlogs, excessive stock build-ups, and obstructed pathways.
These issues can significantly impact warehouse operations and profitability. Order backlogs can lead to delayed shipments, affecting customer satisfaction and potentially resulting in lost sales.
Excessive stock build-ups indicate inefficient inventory management, which can tie up capital and space unnecessarily.
Obstructed pathways pose safety hazards and slow down the movement of goods, further reducing productivity.
Recognizing these signs early allows businesses to take corrective actions, such as reorganizing the layout, optimizing storage solutions, and implementing better inventory management practices.
Solutions to Common Warehouse Storage Problems
Now let us address the solutions.
Build a Mezzanine Floor
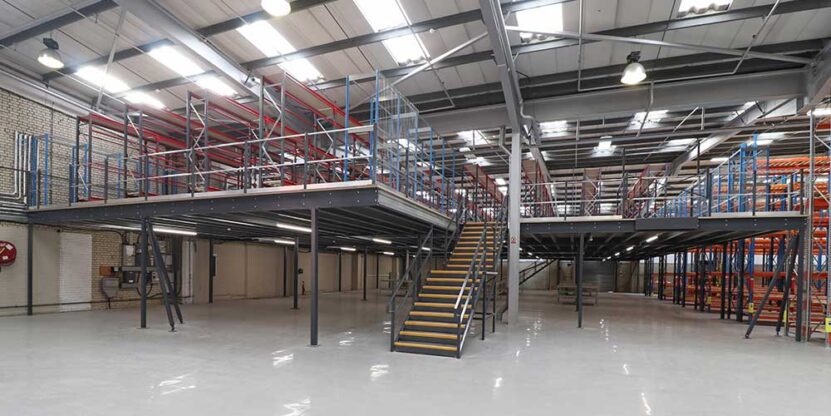
Building a mezzanine floor is an effective solution for creating additional storage space within a warehouse. Mezzanines utilize vertical space, allowing businesses to expand their storage capacity without expanding the warehouse footprint.
The customizable design of mezzanines means they can be tailored to suit specific warehouse needs, accommodating various types of inventory and equipment.
Mezzanine floors can support additional shelving, office space, or workstations, making them versatile and multifunctional.
By effectively using vertical space, mezzanines help maximize storage efficiency, improve workflow, and reduce clutter on the main warehouse floor.
Implement Extra Shelving
Implementing extra shelving, particularly vertical storage solutions, is an excellent way to optimize warehouse space.
Vertical shelving systems, such as Longspan and RET shelving, maximize the use of height, allowing more products to be stored in a smaller footprint. This not only increases storage capacity but also improves organization and accessibility.
Different types of shelving can be used for various inventory needs, from heavy-duty storage for bulk items to more specialized shelving for smaller, more delicate products.
Vertical storage solutions help in maintaining an organized warehouse, simplifying inventory management, and speeding up order picking processes.
Create Mezzanine Office Space
Utilizing vertical space to create mezzanine office space is a strategic way to maximize warehouse efficiency without sacrificing storage floor space.
Mezzanine offices can house administrative functions, meetings, and employee break areas, freeing up valuable ground-level space for storage and operations.
This approach leverages the vertical height of the warehouse, making the most of the available space. By relocating office functions to a mezzanine, businesses can maintain a clear and organized storage area, improve workflow, and enhance operational efficiency.
Mezzanine office spaces can be designed to meet specific needs, ensuring a functional and productive workspace.
Use Pallet Stacking Systems
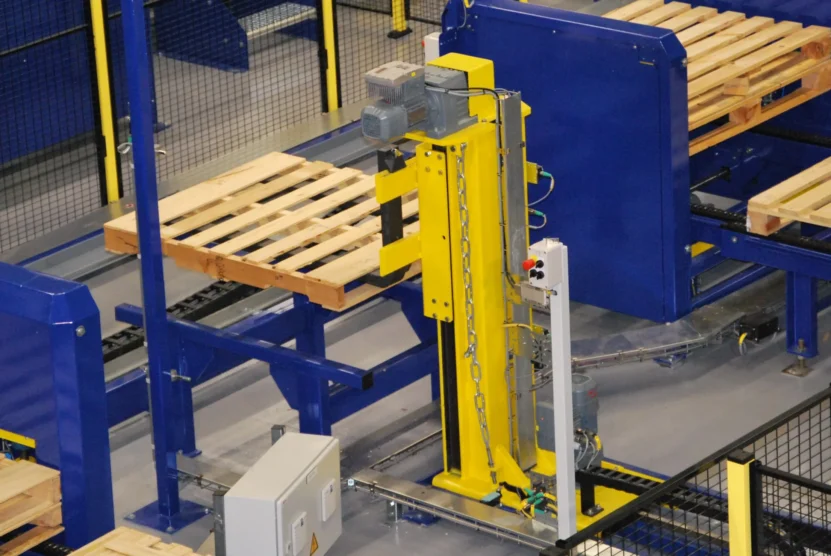
Using pallet stacking systems is an effective way to manage and optimize pallet storage within a warehouse.
Efficient pallet storage options, such as Cantilever Racking, Drive-In Pallet Storage, and Selective Pallet Racking, provide tailored solutions for different storage needs.
In case you need these, be sure to visit https://lenokers.com/production-category/pallet-racks.
Cantilever Racking is ideal for long, bulky items, while Drive-In Pallet Storage maximizes space for high-density storage.
Selective Pallet Racking offers flexibility and easy access to individual pallets, making it suitable for diverse inventory types.
These systems improve storage efficiency, reduce clutter, and enhance accessibility, leading to faster order fulfillment and better space utilization.
Optimize Underused Floor Space
Identifying and utilizing underused floor space can significantly improve warehouse storage efficiency.
Areas that are often overlooked, such as corners, under staircases, and above doorways, can be optimized with:
- Shelving
- Pallet stacking
- Raised storage solutions
By effectively using these spaces, businesses can increase their storage capacity without expanding the warehouse footprint.
This approach not only maximizes space utilization but also helps in maintaining an organized and clutter-free environment.
Properly utilized underused floor space contributes to a smoother workflow, reduces the risk of accidents, and improves overall operational efficiency.
Efficient Space Utilization
Efficient space utilization involves organizing and storing inventory in a way that maximizes the use of available space while simplifying order picking and improving processes.
Storing similar-sized items together and organizing stock based on frequency of use can streamline operations and reduce picking times.
Properly labeling and categorizing inventory helps in maintaining an organized warehouse, making it easier for employees to locate and retrieve items.
Efficient space utilization reduces clutter, minimizes the risk of damage, and enhances productivity.
Re-assess Inventory Management
Re-assessing inventory management practices is crucial for maintaining optimal storage efficiency and meeting customer demands.
Regularly evaluating and improving ordering systems can prevent overstocking or stockouts, ensuring that inventory levels are aligned with demand.
Adapting to demand fluctuations and implementing better inventory tracking methods can enhance accuracy and reduce the risk of errors. Utilizing modern inventory management systems can streamline processes, improve order accuracy, and provide real-time visibility into inventory levels.
Effective inventory management helps in maintaining an organized warehouse, reducing holding costs, and improving customer satisfaction.