Cobots, or collaborative robots, are transforming industries by bringing automation, precision, and efficiency to new heights. Unlike traditional industrial robots, cobots are designed to work alongside humans, handling repetitive and precise tasks in manufacturing, logistics, and beyond. But getting the most out of a cobot’s capabilities requires careful optimization with high-quality parts and accessories.
The Role of End-Effectors in Cobot Precision
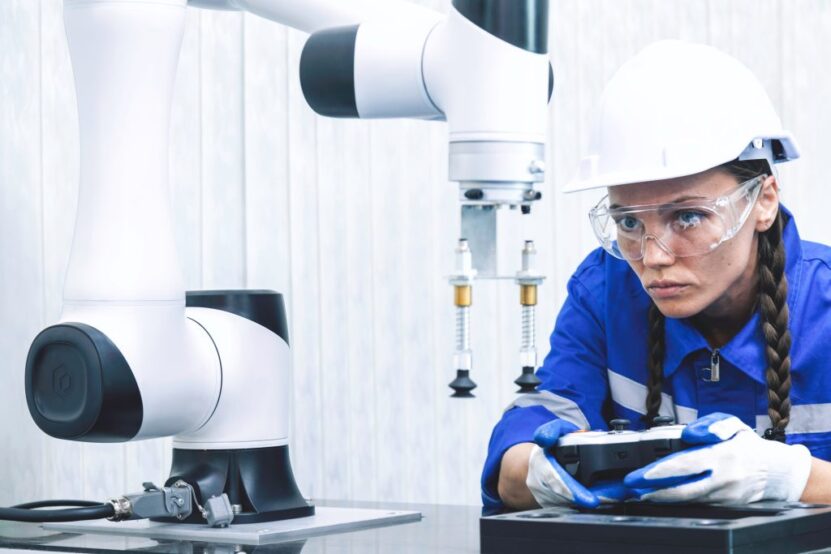
End-effectors are the tools or devices attached to a cobot’s arm, enabling it to interact with objects or perform specific tasks. Whether it’s gripping, welding, screwing, or assembling, end-effectors are crucial for cobot functionality. By selecting the right end-effector, companies can enhance the accuracy and versatility of cobots in their workflows.
There’s a wide range of end-effectors, each designed to handle specific tasks with precision:
- Grippers: Used for handling objects, grippers can vary based on the material they are handling. Vacuum grippers, for instance, are often used in packaging, while two-finger grippers are effective in delicate assembly tasks.
- Welding Tools: For manufacturing sectors where welding is a core operation, welding end-effectors are designed to precisely weld materials with minimal human intervention.
- Screwdrivers: Cobots equipped with screwdrivers are ideal for assembly lines that require consistent torque for screws in electronics or automotive parts.
Force and Torque Sensors for Improved Accuracy
Force and torque sensors play an integral role in enabling cobots to handle delicate or sensitive tasks. By measuring applied force and torque, these sensors allow the cobot to adjust its actions based on environmental feedback, reducing the risk of damage to materials.
When selecting a force and torque sensor, focus on sensitivity, compatibility, and calibration ease. A highly sensitive sensor ensures that even the smallest adjustments are accounted for, which is crucial in applications like polishing or assembling fragile components.
3D Cameras for Enhanced Spatial Awareness and Precision
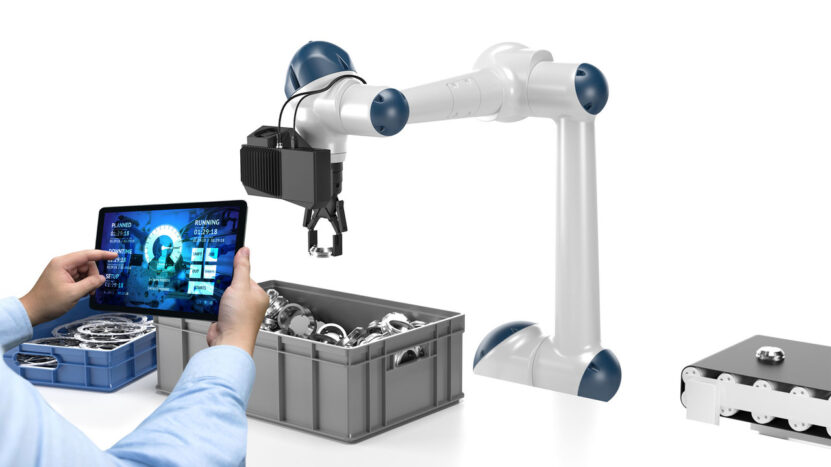
For cobots to work in dynamic environments with high levels of accuracy, 3D cameras have become essential. By providing cobots with depth perception and spatial awareness, 3D cameras allow cobots to “see” their surroundings and adjust actions based on object positioning and distance. Companies like Mech-Mind Robotics, for example, bring industrial automation to the next level with 3D cameras that improve the efficiency and precision of cobots.
3D cameras capture spatial data in real-time, enabling cobots to adapt to variations in object positions, identify different shapes, and avoid obstacles. This technology is particularly beneficial in pick-and-place tasks, where items may not always be in the same spot, and the cobot must adapt to new conditions.
Vision Systems and AI Integration for Real-Time Decision Making
Beyond 3D cameras, advanced vision systems equipped with AI capabilities allow cobots to interpret complex data, recognize patterns, and make decisions in real-time. Vision systems, combined with AI algorithms, help cobots adapt to tasks with greater efficiency.
A comprehensive vision system includes high-resolution cameras, sensors, and processing software. This combination enables cobots to “see” beyond what traditional sensors detect, like differentiating between defect-free and defective products. The AI component helps the cobot learn and improve its efficiency over time.
Precision-Enhancing Software and Algorithms
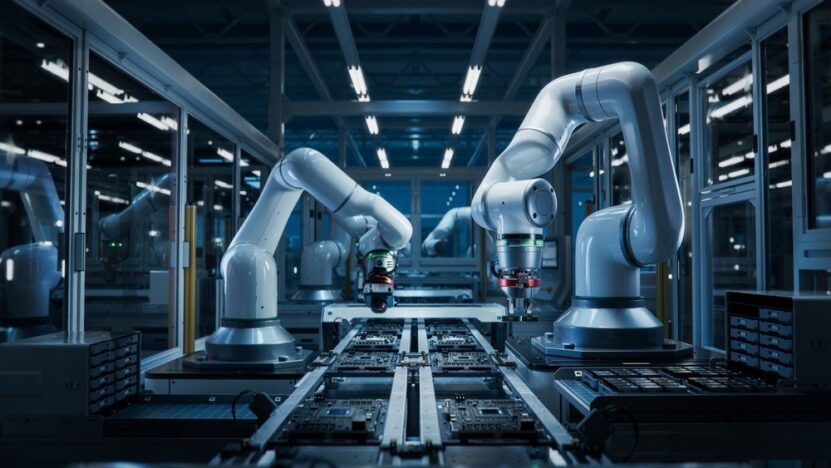
Software plays a pivotal role in fine-tuning cobot movements, enabling them to execute tasks with precision and reliability. Specialized algorithms can also correct for minor deviations, further improving efficiency and reducing errors.
Precision-enhancing software can include:
- Path-Planning Software: Optimizes cobot movements, allowing them to follow the most efficient path with minimal deviations.
- Error Correction Algorithms: Continuously adjust cobot movements to compensate for external factors, such as vibrations.
- Machine Learning Integrations: Cobots can learn from repeated tasks and make incremental adjustments over time.
Collaborative Safety Systems for Operational Efficiency
Safety is paramount in environments where humans and cobots work side by side. Collaborative safety systems ensure that cobots operate without posing risks, enabling humans and robots to work seamlessly in shared spaces.
- Proximity Sensors: Detect when humans are nearby and automatically slow down or stop the cobot’s movements to prevent accidents.
- Emergency Stop Mechanisms: Allow operators to stop the cobot immediately in case of an emergency.
- Safety Programming: Software that configures safe zones, where the cobot operates within a restricted range when humans are present.
Safety systems allow cobots to perform tasks continuously, only adjusting movements when necessary. This minimizes downtime, making workflows more efficient while keeping the work environment safe.
Maintenance and Calibration Tools for Longevity and Precision
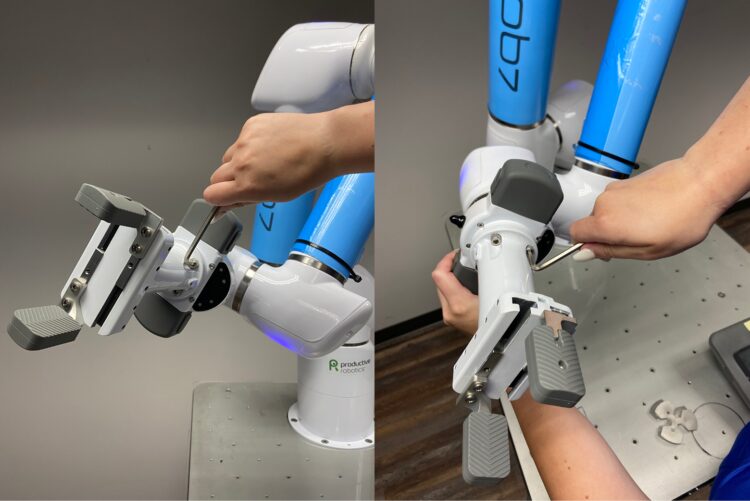
Routine maintenance and precise calibration are essential to keep cobots running smoothly and maintaining accuracy. Cobots are high-investment tools, so regular upkeep protects that investment.
Regular maintenance includes checking joints, lubricating moving parts, and inspecting end-effectors. Identifying wear and tear early on can prevent more significant issues that disrupt workflows.
Calibration is vital for keeping sensors, cameras, and end-effectors in sync. Specialized calibration tools, such as laser-based measurement systems, help ensure that every component is working in alignment, maintaining high precision.
Conclusion
Achieving precision and efficiency with cobots requires investing in high-quality parts and accessories, each tailored to enhance specific aspects of performance. From end-effectors that enable task-specific versatility to 3D cameras that offer spatial awareness, these components are vital for maximizing cobot efficiency in modern industries. Investing in the right parts will enhance productivity and reduce the risk of costly errors. With advancements in 3D cameras, cobots are primed to meet the evolving demands of industrial automation.